/dd-tools/dd-tools-light/dd-tools-light-motors/dd-dd-150-u-diamond-coring-tools/203113.png)
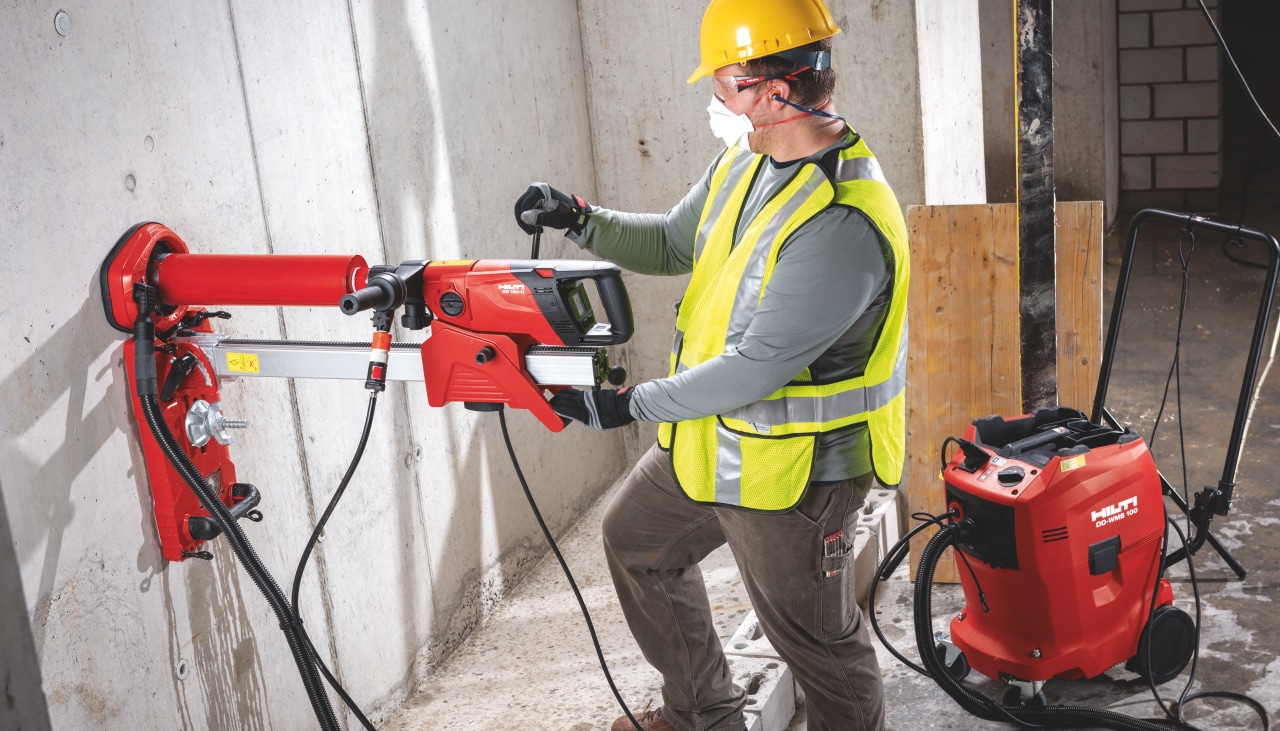
Control construction dust
Improve working comfort, safety and productivity with Hilti Dust Removal Systems (DRS)
/dd-tools/dd-tools-light/dd-tools-light-motors/dd-dd-150-u-diamond-coring-tools/203113.png)
Everyday construction jobs – such as grinding, cutting, drilling, breaking and chasing – may create hazardous dust which can negatively impact health and safety but also jobsite productivity. In addition, construction dust does not just stay at the jobsite, but can spread to other areas impacting people, nature and the environment.
Many of the harmful dust particles created are so tiny that they are barely visible, and the smaller they are the longer they take to settle. For example, a 0.1 micrometer dust particle can take more than 12 days to settle on the floor from a height of just one meter [1]. This is why on jobsites, even when we don’t see construction dust, we can still smell it – if you think a room smells “like concrete”, it's probably because of microscopic concrete dust particles circulating in the air.
Dust can pose a threat to Health and Safety
No-one in the construction industry wants to expose team members to unnecessary hazards, but the longer a worker is exposed to dust, the more risks posed to their health and safety.
Silica dust particles – found in concrete, tile, brick and mortar – can cause cancer and incurable silicosis if long-term overexposure reaches the lungs’ air sacks (alveoli). Exposure to silica dust particles may also cause and possibly worsen cases of asthma.
Dust can impact nearly every stage of the job
As well as reducing productivity through illness and sick leave, dust can impact nearly every stage of construction jobs:
- Wasting time: sealing off areas before starting work
- Damaging fixtures and fittings: such as carpets, furniture and other furnishings
- Affecting other work: such as plastering, painting and electrics
- Delaying handover: time-consuming clean-up work afterwards
Less noticeably, construction dust can also clog up tools by getting into motors and other working parts, which can lead to high repair costs and frustrating downtime. Dust particles also collect on sharp elements of inserts - such as chisel tips, drill bit edges and grinding disc surfaces - possibly making them blunt and shortening their life span.
As well as posing a threat to your team’s health and safety, concrete dust can also impair working comfort by reducing visibility, causing coughs and sneezes, irritating eyes and clogging clothes, hair and mobile phones. Working to reduce exposure to hazardous dust not only makes working conditions better, but it also boosts productivity thanks to a more comfortable working environment.
Substitution: eliminate the risks of dust by using alternatives
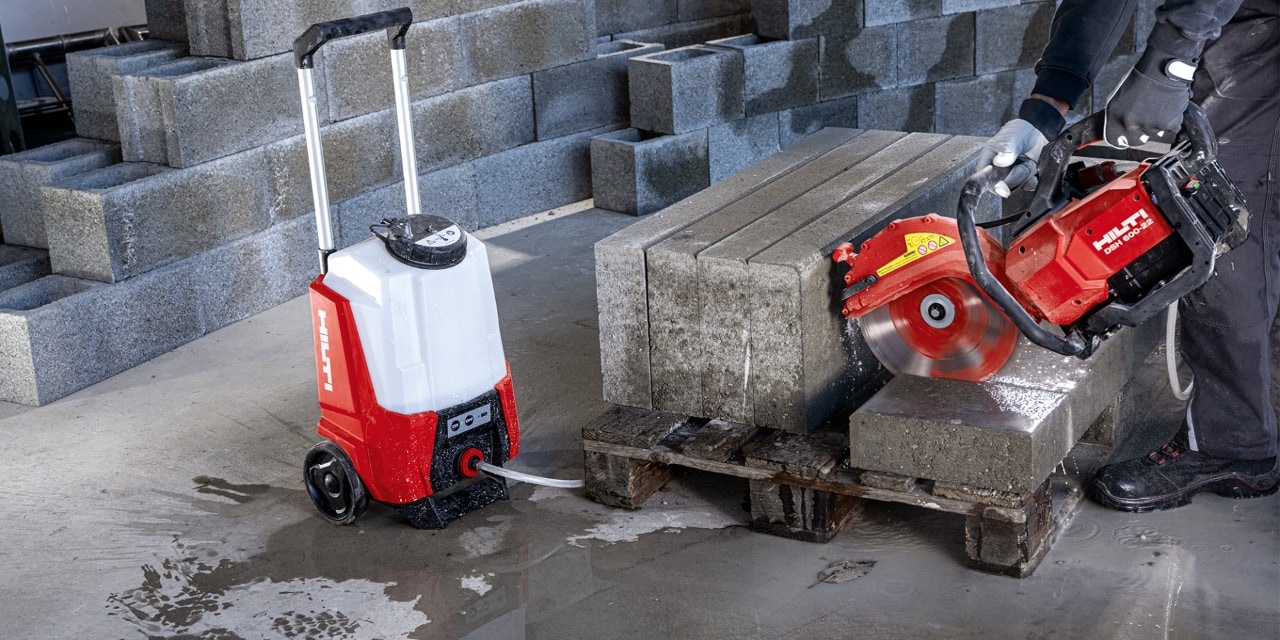
Wet diamond drilling
Get more done per tank – water flow responds automatically to the opening and closing of the water valve on the tool, significantly reducing wasted water and interruptions to refill the tank
Water supply unit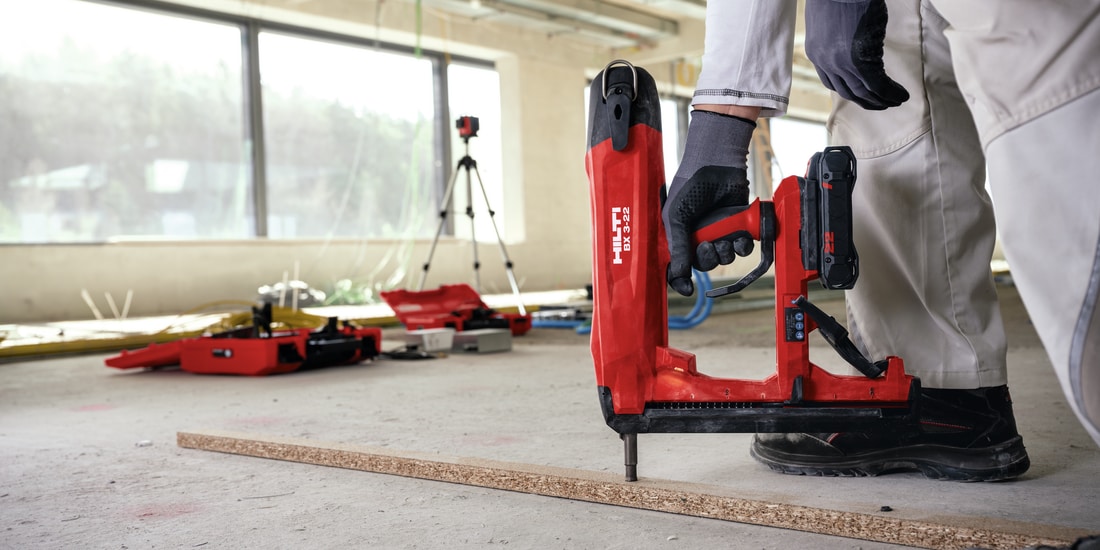
Direct fastening
Make the switch to the BX 3 battery-powered nailer, designed to be a cleaner, quieter and virtually dust-free alternative to drilling.
BX 3 battery-powered nailer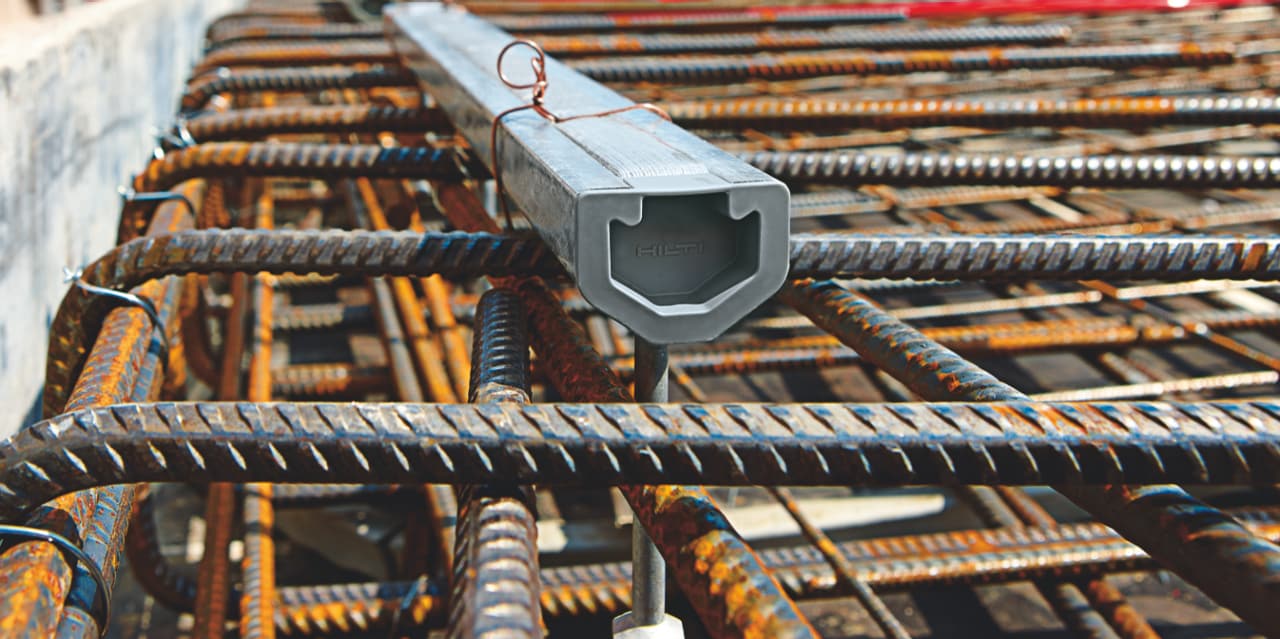
Designing out concrete dust
Choose low-dust base materials or place our HAC cast-in anchor channels around the rebar before the concrete is poured, meaning little to no drilling, and therefore no concrete dust.
HAC cast-in anchor channelsPersonal protective equipment: where health risks remain
Lastly, if there is no way for tradespeople to remain below dust limit values, then it’s important to use relevant personal protective equipment (PPE). Dust masks, eye protection, disposable overalls and gloves are all essential kit, even when using virtually dust-free tools. In conditions where dust levels are unavoidably high, respirators may be necessary for maximum protection against dust inhalation.